THANK YOU FOR SUBSCRIBING

An Integrated Approach for Next-Generation Bioprocessing
Somasundaram Gopalakrishnan, Senior Technical Consultant Process Solutions – Apac, Merck Life Sciences

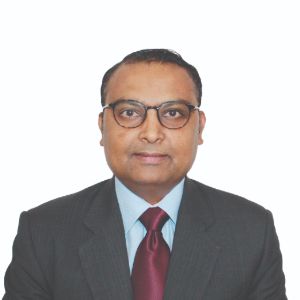
Somasundaram Gopalakrishnan, Senior Technical Consultant Process Solutions – Apac, Merck Life Sciences
The biopharma landscape is evolving. The move towards next generation bioprocessing - including intensified and continuous processing - is happening now and it impacts all of us: Customers are seeking new strategies to deliver higher productivity, improved economics, greater flexibility, and enhanced quality and safety. Suppliers are developing novel technologies and game-changing solutions and regulatory agencies are helping to safeguard the way forward.
This is why the BioContinuum Platform (formerly known as Next Generation Bioprocessing) was brought to life. It represents our belief in and commitment to this evolution in bioprocessing.
Current trends in the biopharmaceutical industry, including continued market growth, the arrival of new product groups, cost pressures and the trend towards localized manufacturing are exerting unprecedented pressure on bio manufacturers to innovate bio manufacturing platforms.
Continuous processing is usually portrayed as an ideal destination, one where costs are lower, footprints are smaller, system assembly is faster and easier, and operations are more secure and less prone to error. This destination, however, lacks a common approach. That is, different would-be implementers of continuous processing have different starting points. Some implementers plan to build all-new facilities. Others need to retrofit existing facilities. Some want to approach continuous processing piecemeal. Others want to adopt end-to-end solutions.
In 2017, the BioPhorum Operations Group, a cross-industry collaboration, released its technology roadmap with some “very aspirational goals” for biopharmaceutical manufacturing. Among these goals are vast reductions in footprints, capital expenditures, construction times, and operating expenses. And while some wholesale changes lie ahead, industry can in the meantime effect more evolutionary changes to increase productivity.
Merck KGaA/MilliporeSigma’s (within USA/ Canada) BioContinuum™ Buffer Delivery platform is an integrated, configurable system that incorporates distinct buffer concentrates, single-use assemblies, an automated buffer dilution system, and tailored system services. The system is designed to expedite accurate and precise buffer preparation and management.
Continuous processing can help a bio manufacturer achieve many laudable goals, including greater efficiency, flexibility, and robustness; smaller equipment and facility footprints; better product quality; and real-time product release
There is a lot of interest around process analytics, software automation, and single-use components. Additionally, the perfusion bioreactor and continuous capture have already received lot of attention. Supporting processes and additional unit operations will become increasingly important focus for manufacturers looking to cut costs, mitigate risk, and become more efficient.
On the upstream side, reducing risk through the use of a high cell density cryopreservation in the seed train, which in turn, allows separating a process intermediate from the seed train, perhaps performing some operations off site, and enabling closed processing of the seed train once on site. Another area for potential improvement is using perfusion in the N-1 bioreactor, allowing a far higher seed density into the final (production) bioreactor and, therefore, the same productivity in a shorter production time.
One by product of more efficient, intensified processes is higher titers. Downstream buffer volume increases linearly with bioreactor titer, and that greater volume must be accommodated, often without any increase in available space. The automated skid-mounted BioContinuum platform uses buffer concentrates of 10×, 20×, and even 50× to provide all the chemical composition in a much smaller footprint.
Concentrates are QC released prior to use and diluted with the plant’s own water for injection into hold vessels. The 1× buffers can then be transferred around the facility. Process intensification via buffer delivery is fast and flexible; avoids powder, dust, and debris; and is “incredibly accurate and precise.” And best of all, it reduces labor costs and increases operator safety.
Companies looking to intensify their processes, the final dream goal, the final step, is going fully continuous upstream: having a very high cell density process, which is run consistently, for a long period of time.
Continuous processing can help a bio manufacturer achieve many laudable goals, including greater efficiency, flexibility, and robustness (by reducing the number of steps and holds); smaller equipment and facility footprints; better product quality; and real-time product release. The key is an integrated approach. Critical quality attributes (CQAs) need to be identified, and the functional relationships that link the critical material attributes (CMAs) and critical process parameters (CPPs) to the product CQAs need to be understood.
Knowing the product—including the CQAs of both the drug and its excipients—and how it’s made, and the potential impact of the CQAs on safety and efficacy, can allow more flexibility in the regulatory process. The bio manufacturer can demonstrate that it knows and can control what matters.
The industry is looking forward to produce huge amounts of biologics to treat different diseases and indications including cancer, and continuous operation will probably be the best approach to produce such large quantities. Merck is in a right position to support the Biopharma customers to realise their DREAM!
Weekly Brief
I agree We use cookies on this website to enhance your user experience. By clicking any link on this page you are giving your consent for us to set cookies. More info
Read Also
