THANK YOU FOR SUBSCRIBING

Recent Advancements in Service Technology: Changing the Game in Healthcare Service
Jaco Bierman, Head of Service Operations, GE Healthcare

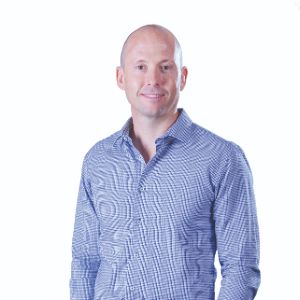
Jaco Bierman, Head of Service Operations, GE Healthcare
When buying new healthcare equipment, today’s customers are not just looking at the patient outcomes, which technology can help them achieve. They are now placing a huge amount of value on the total-cost-of-ownership as well as the associated customer service benefits that an original equipment manufacturer (OEM) can offer. When faced with a similar product technology offer from two competing companies at a comparable price range, the customer will almost certainly base their purchasing decision on the company that can guarantee the lowest downtime at the most aggressive price point over the usable lifetime of that piece of equipment. This has (or, at least should be) the focus of medical equipment manufacturers all over the world. How do you guarantee the lowest unplanned downtime on a piece of equipment at the most affordable price to your customer?
Recent Advancements in the Healthcare Service Environment: Cracking the Ultimate Challenge of Guaranteeing Zero Unplanned Downtime on Healthcare Equipment
Healthcare equipment produces huge amounts of data; not only patient or image data but serviceable usage data. In parallel, most of the healthcare equipment have been designed to enable remote connectivity for many years now. OEMs are using this remote connectivity in very innovative ways to proactively predict failures before they occur, as well as reactively resolve any failures remotely that have occurred. Systems are programmed to scan and record data linked to usage and environmental conditions in a myriad of ways. This data is then used to predict when the next system failure would occur. Companies use this data to either ensure that they have the parts, resources and tools available at the time of failure or in some instances, would replace certain parts proactively based on this predictive data to ensure no unplanned downtime to the customer. Certain parts like X-ray tubes, in most conditions, have an average estimated lifespan measured in the number of exposures or scan seconds. Using this data, linked closely with other parameters monitored via various system logs, OEMs can predict to a certain level of accuracy when that X-ray tube could fail.
Remotely Logging into Systems After a Failure has Occurred is in No Ways New Technology However, we are seeing increasing trends of remote capabilities of new healthcare products where 4050 percent remote fix rates are now possible. Imagine, as an OEM, that one out of every two customer’s calls could be remotely resolved in less than 1 hour without the need to dispatch a field engineer (FE). The customer would not need to reschedule a patient list and could use the time saved to more effectively focus on patient outcomes.
Today’s healthcare equipment customers focus on its total-cost-of-ownership as well as the associated customer service benefits "quality and consistent customer service— a key differentiator in the global healthcare environment
That being said, if a remote fix is not possible, it is of absolute importance to ensure that the right field engineer with the right capabilities located closest to that installed base is dispatched. In Southeast Asia, GE Healthcare uses an application called Smart Dispatch Tool (SDT),which allows us to track the whereabouts of the FEs, their work schedules as well as their expertise and training records. This, in turn, allows us to dispatch the most suitable FE located closest to the equipment, ensuring that we not only decrease the response time to the customer and minimize the downtime but also, from a business perspective, reduce travel costs and maximize utilization of our field team.
Another noticeable trend is that the field force is increasingly becoming multi-skilled. As there mote capabilities of equipment increases, we are seeing more expert online engineers assisting the FEs. In parallel, we are noticing a shift to more multi-modality trained FEs in the field able to work across various areas of the medical portfolios such as radiology to ultrasound, and life support equipment. This results in various benefits to the customer as they are able to access small centers of support around dense installed base areas. This is a critical benefit in Southeast Asia where access to healthcare services is fragmented across rural and urban areas, and where demand outstrips supply in major cities. Gone are the days of FEs being a one-modality expert.
TRACE is another tool used by GE Healthcare to manage the effective and impactful cross-modality support deployment. This tool uses geolocation functionality to map installed equipment as well as FElocations across the region. It keeps track of the service history of each piece of equipment, thus, enabling us to determine the utilization and travel ratio per FE. Using this data, we can then evaluate the extent to which we can reduce travel time by cross-training an FE to support across various modalities.
Although the benefits of these advancements linked particularly to quicker response times, less downtime as well as cost efficiencies cannot be ignored, they do not come without their inherent challenges. Firstly, there will be a prevalent risk of cyber-attacks when any piece of equipment is connected to the internet. We have seen an increase in cases of bad actors targeting medical equipment globally as they contain sensitive patient data and information. GE Healthcare has been investing heavily in cyber security prevention and protection globally, from the product development stage for new technologies, all the way to working with customers to find solutions for existing systems. While there is no foolproof solution to this developing trend yet, we are also glad that more customers are taking precautions to safeguard against vulnerabilities and collaborating with their vendors to share insights to protect their patients together.
Secondly, when first introduced in any environment, remote and digital service delivery will require a fundamental change in culture and expectation of customers. Customers need to realize that they will not always have physical support onsite whenever they log a service call. They will need to trust the experience and capability of the online engineer whom they do not physically see. Finally, when giving customers access to data, service providers need to make sure it is accurate and reliable. Customers can now use applications to see, for instance, when an FE will be onsite, when the parts will arrive or even how long the equipment was down for. This data is obtained from various sources but ultimately dependant on human behaviour to input accurate data in a timely manner.
In conclusion, there are so many new technologies on the horizon that can enhance service delivery in the healthcare environment. In the end, it all comes down to building a well-rounded customer experience based on knowing what the target customers perceive as value.
Weekly Brief
I agree We use cookies on this website to enhance your user experience. By clicking any link on this page you are giving your consent for us to set cookies. More info
Read Also
Where Technology Meets Tradition in Sports
Why Software Delivery Centres Fail In Insurance
Building Smarter Content Systems for Scalable Growth
The Thoughtful Innovation behind Every Loaf
Lessons for Ambitious Professionals in a Digital World
Designing For Regeneration, Not Just Resilience
Listening Beyond Hearing
Modernizing Lending Through Innovative, Secure and Scalable Technology
